Thermo-Compression Molding of a Hybrid Electric Vehicle (HEV) Duct for the Automotive Industry
Calling on our thermo-compression molding expertise for parts for the automotive industry, S&A Industries was contracted to manufacture this custom inlet and discharge duct. The compression porous duct was designed for noise reduction within a battery cooling application for hybrid vehicles. The purpose is to bring cooled air to the ESS from the cabin without creating a noise issue for the passengers. This thermo-compressed duct project allowed us to exhibit our many capabilities beyond thermo-compression including non-woven material production, hot plate welding, gluing, in line testing and complex assembly. Producing and utilizing recyclable non-woven polyester provided a 35% weight reduction compared to a plastic duct. It also afforded a temperature resistance up to 95°C and breathability of 10l/dm2/min/mbar. The duct,
used globally for hybrid and electric vehicles, offered safety features to protect the expensive batteries used in the specialty vehicles. The noise performance of the part speaks for itself. The Inlet porous duct yielded 10dB improvement compared to a molded duct. The discharge porous duct yielded up to 5dB at higher frequencies.
Upon delivery of the duct, our customer was pleased with all of the product benefits while the part met automotive interior requirements and customer provided standards. To see how S&A Industries can thermo-compress the perfect part for your application, contact us.
Thermo-Compression Molding Project Highlights
Inlet & Discharge Porous Duct Manufacturing | Compression Porous duct is used for noise reduction within a Battery Cooling Application for Hybrid Vehicle | |
---|---|---|
Capabilities Applied/Processes |
| |
3D & Modeling capability | Software Capabilities :
| |
Material Used | Non-Woven Polyester | |
Technical Specifications |
| |
Features / Advantage |
| |
Noise Performance |
| |
Industry for Use |
| |
Delivery Location | Globally | |
Standards Met | Automotive Interior requirements | |
Product Name | Porous Noise Reduction Duct |
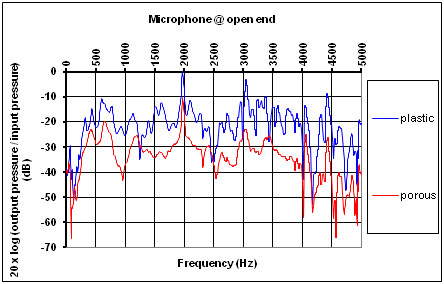